We use automation to create new opportunities, not to replace people
You may have seen reports from MIT researchers that say that – on average – each robot added to manufacturing replaced 3.3 workers nationally and lowered wages. There’s a lot more to the data than that, so be sure to check out more details on the study on the Robotics Business Review.
While we can’t speak for other industries or manufacturers, we can say that automation and robotics enhance the jobs of our employees and lead to more, sustainable jobs in the long run.
In fact that’s one of our core beliefs: We don’t treat people like robots, we give people robots to use.
“Anytime there’s a person sitting in a chair doing a repetitive operation, it’s violating that principle,” US Digital CEO and Founder David Madore said. “Tedious tasks are better performed by robots. We don’t always start that way but we end up that way as we progress.”
Over the years we’ve found putting more effort into improving internal systems, automation tools and employee training pays great dividends back on the investment, Madore said.
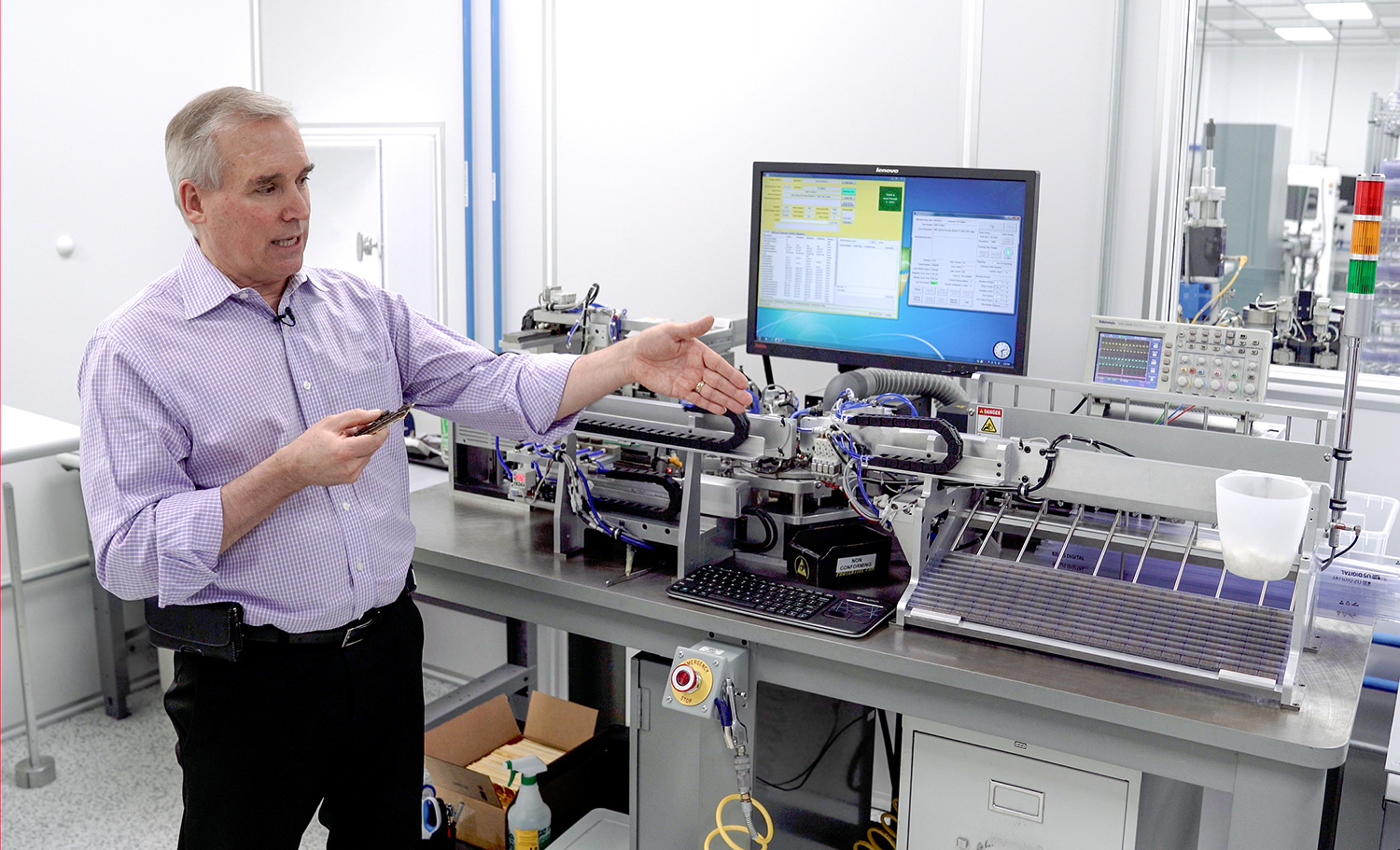
So how does it play out in real life? Let’s look at our cleanroom as an example.
In 2009 we had 4 specialists working in the clean room assembling encoder modules by hand.
At the end of the year, our employees were able to assemble about 40,000 modules. It was an impressive feat, but not something that was sustainable long-term, particularly if we were going to be using the modules in most of our products in the future.
“We asked ourselves if there was a better way to be doing this,” US Digital COO Neal Donowitz said. “The answer was, of course, yes.”
US Digital engineers designed automated machines that now handle encapsulation, wire and die bonding, inspection, marking and packaging of the modules. People are there to feed the machines, make sure they are performing as expected and do visual inspections that are better suited to the human eye.
Last year we produced more than 1,000,000 encoder modules using various automation systems. We now have seven full-time cleanroom technicians who visually inspect parts and help us solve problems and further streamline our processes.
“We often ask ourselves not only how we can work smarter, but we ask why we do things the way that we do,” Madore said. “That leads to new opportunities for improvement.”
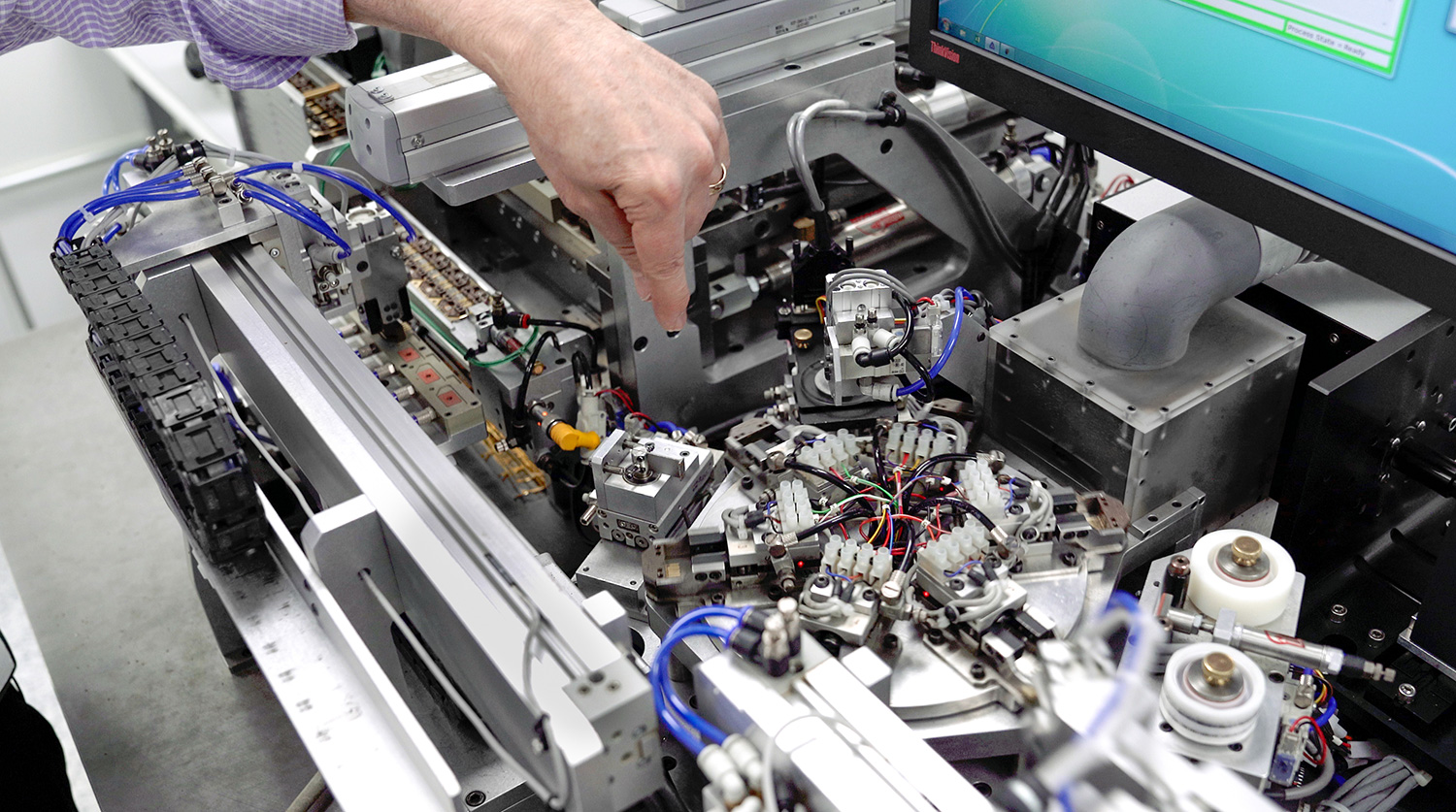
In this case, automation allowed us to increase our manufacturing capability 25X, promote the four original employees and hire three additional ones, and all along keep our focus on providing our customers with high quality cost competitive solutions.
If we hadn’t used automation, we’d need to have something more like 100 employees to do the same job, not to mention the additional space required for that many people. That wouldn’t be feasible from a cost perspective and we would have either not grown the business or looked to outsource the manufacturing to somewhere with cheaper labor, like so many other manufacturers are doing these days. Now we’re set up for growth.
“American manufacturers will not successfully compete in the world market if human fingers are doing the assembly with mind numbing repetition,” Madore said. “But the cost for automation is the same worldwide and jobs are more satisfying when people get to work smarter. We continue to grow and provide more and better jobs by designing and equipping our team with fascinating automation machines to do the tedious work. It’s a lot more fun and satisfying.”
And that fun never ends. Our in house engineers are working on updated versions of some of the machines in our clean room that will further increase our efficiency and create more room for future growth.
More in News
Stay up to date
Sign up for our newsletter to stay up to date with our product updates, blog posts, videos and white papers.